Reference:
Thöni Pfaffenhofen
New gas/induction heater with hot saw in the patented “in-line” design, an ageing oven system, and a new die heater at the Pfaffenhofen plant.
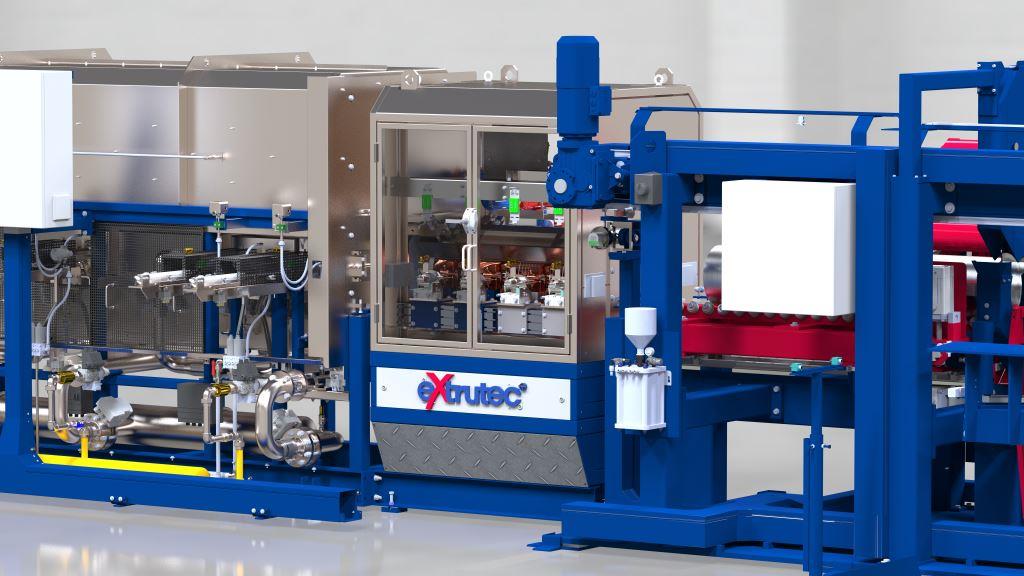
Tasks/Project Requirements:
Construction of a state-of-the-art extrusion plant with various further processing facilities at the new Pfaffenhofen plant included an order from extrutec for the delivery, assembly, and commissioning of a new gas/induction heater with hot saw in the patented “in-line” design, an ageing oven, and a new overheat die heater. The customer installed a new 12"-55MN extrusion press in its extrusion line, while an entirely new outlet device and additional equipment for various further processing steps were placed downstream of it. extrutec’s task was to integrate a new “state of the art” billet heating system with integrated induction component and downstream hot saw into the overall concept. Furthermore, extrutec was charged with installation of a fully automatic 8-chamber die heater as well as an ageing oven facility (4+1 ovens) specifically developed for this order for the quenching and annealing of standard lengths and overlengths up to max. 14,000 mm alike. Both heaters are designed as overhead versions with service shuttle and the heating material is loaded fully automatically from below into the heater chambers.
Implementation:
The billets are fed to an automatic chain magazine with two separately powered chain strands in order to comply with the specification for production with lowest noise development. Once the billets are transferred to the heater charging system, they are preheated in the ESU (Eco Shower Unit). This system, for which a patent is pending, uses the residual heat from the exhaust gases of the gas heater and generates water heated to up to 90 °C (195 °F) in an air-water heat exchanger. This is then directed onto the billet surface, which preheats the billets accordingly.
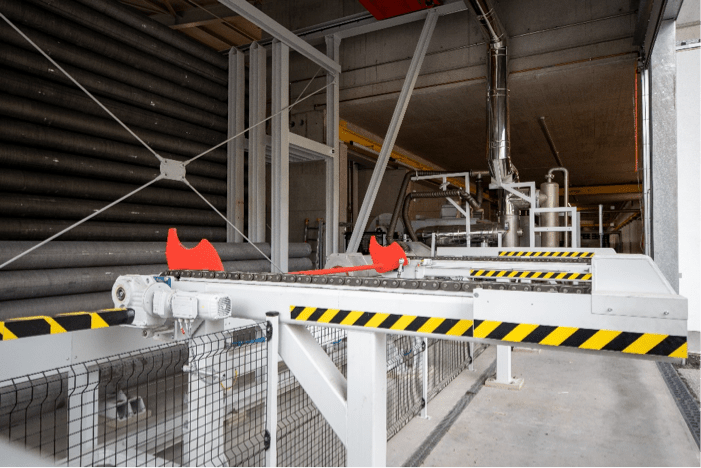
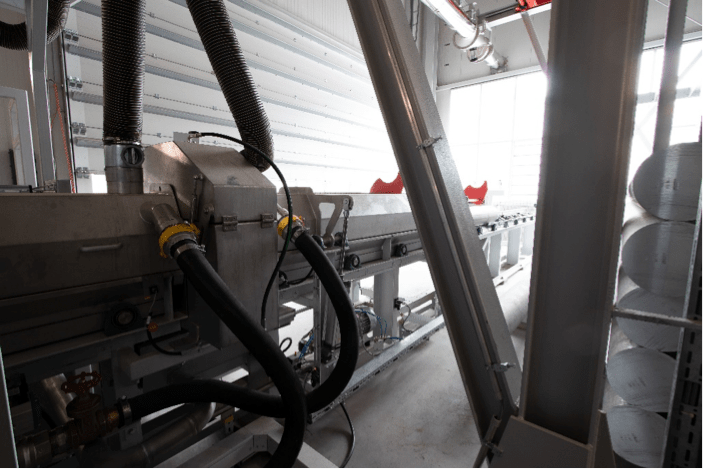


This preheating method not only saves up to > 10% of energy but also achieves an equally high performance increase of the heater system and reduces emissions. The billet preheated in this manner then pass through a billet cleaning system integrated in the ESU, where the billets are cleaned with hot water at a pressure of 210 (3000 psi) bar and a water temperature of approx. 90 °C (195 °F).
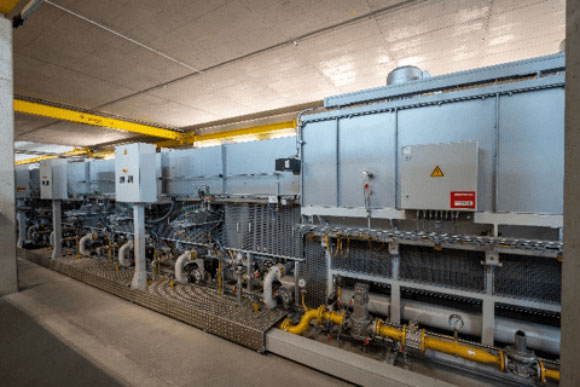
After preheating to approx. 90 °C, additional heat is introduced into the billets in the downstream preheating zone.
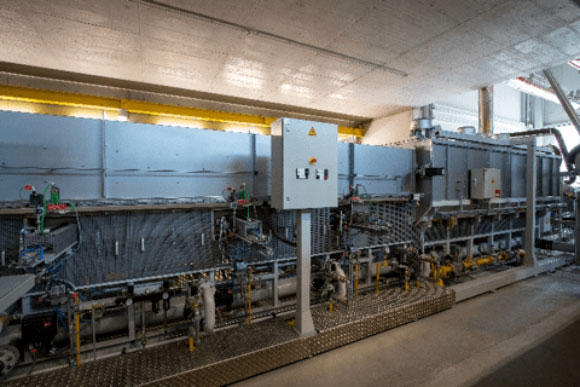
Then heating to the required basic temperature of approx. 400 °C (750 °F) takes place in the directly gas-heated section of the quick-heating furnace.
A high-precision temperature taper, which is indispensable for current extrusion processes, is then applied in a new induction heater (external purchased part), which is integrated “in-line” between the gas heater and the hot saw.
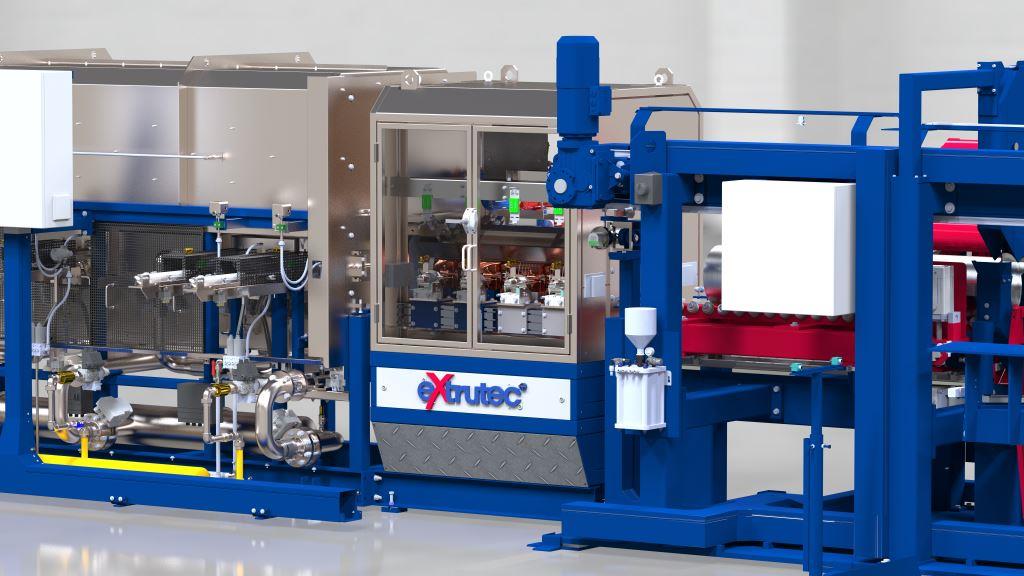
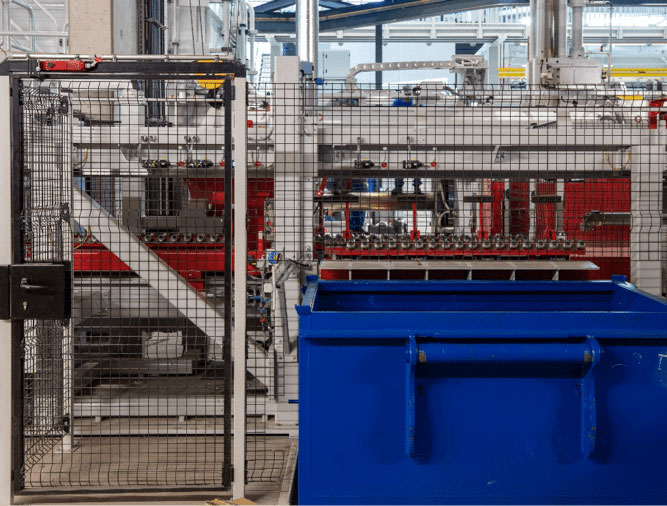
After being optimally pre-heated here, the log is then precisely cut in a hot saw and fed to the press loader of the new extrusion press.
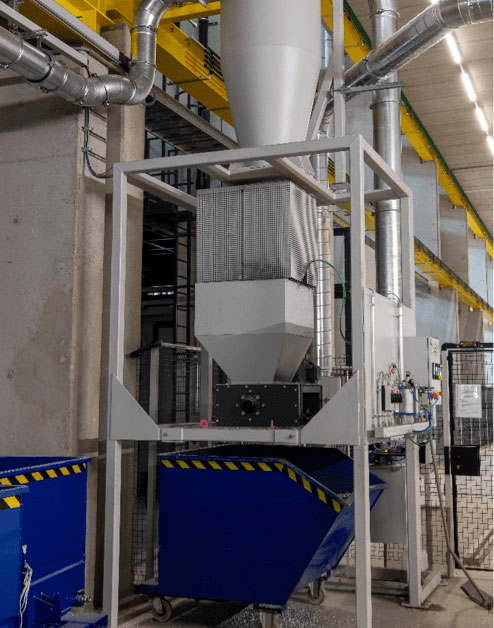
The resulting chips are extracted by a high-performance chip extractor.
Implementation of the Die Heater in Overhead Design with Shuttle:
In the field of die heating, Thöni has chosen to install a new fully automatic 8-chamber overhead die heater from extrutec. This ensures the highest temperature tolerances and, in addition to a generous heating capacity of 8 dies at the same time, also offers “on-board” storage space for 5 additional cold dies needed for the jobs pending next.
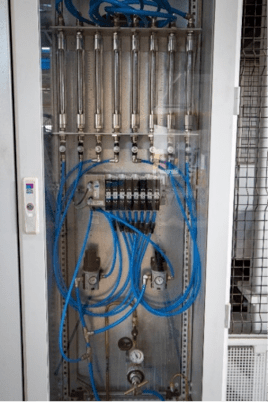
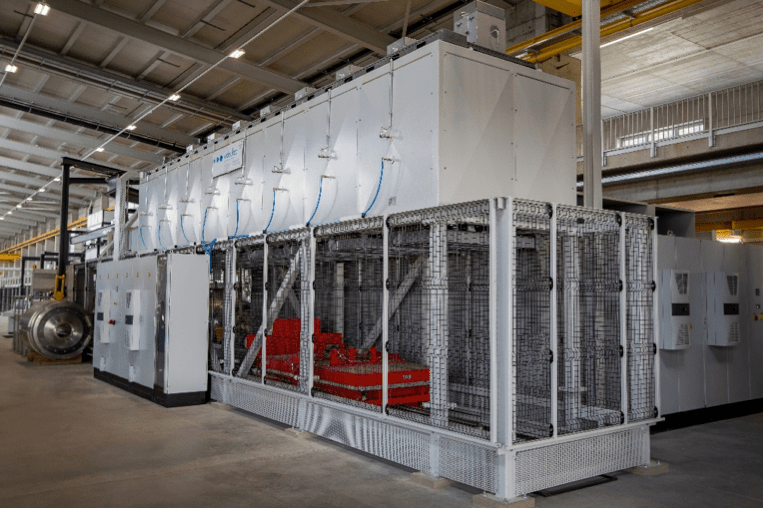
All chambers of the die heater are designed for operation with a protective gas atmosphere (nitrogen). The casting rings of the individual chambers are welded gas-tightly to minimise the consumption of the expensive protective gas.
Implementation of an Overhead Ageing Oven with Shuttle:
Annealing of the pressed profiles is carried out in an extrutec ageing oven, which was designed in an energy-saving overhead arrangement. A total of 4 single heaters for a maximal profile length of approx. 8,200 mm as well as a double heater for the annealing of overlengths (14,000 mm) were delivered. The respective heaters are charged and discharged by way of a rail-bound shuttle that picks up the individual heater charges (2x4 baskets) from one of the buffer stations and places them on the lowered heater bottoms.
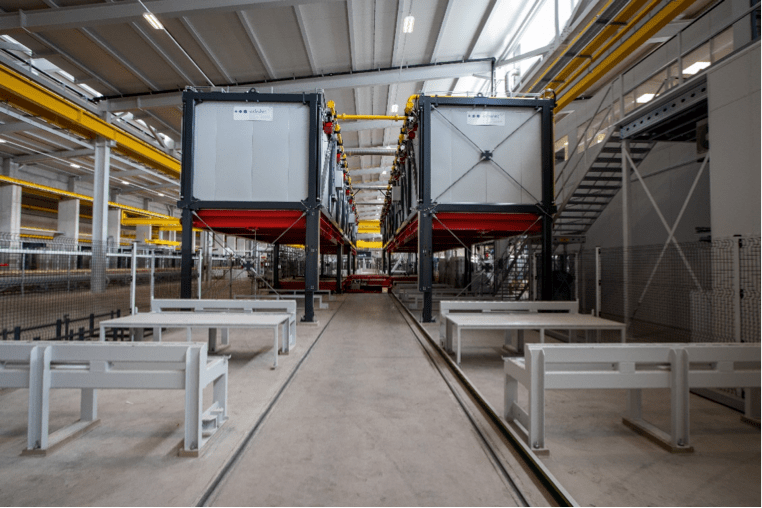
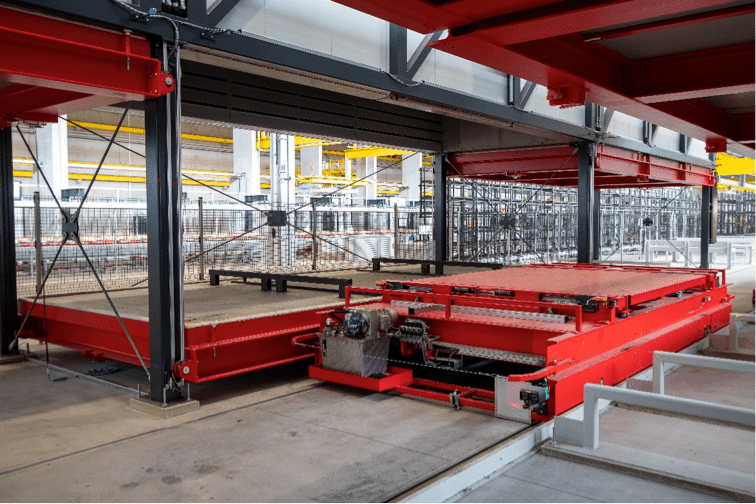
The heater bottoms are closed by 4 hydraulic cylinders per heater instead of the scissor lift tables otherwise common in this application. After quenching and annealing, the heater bottoms with the finished charge are lowered, taken over again by the shuttle, and parked in the designated storage area. 2 x 8 of these deposit benches are installed as buffer stations up- and downstream of the ageing ovens in order to ensure the corresponding production flexibility. Delivery of baskets for quenching and annealing as well as collection of baskets with fully quenched and annealed material is performed by an automatic crane installed by the customer, controlled by an associated control system to the corresponding buffer stations.
Installation and subsequent commissioning of the plant took place in May 2019.
For a detailed list of our reference plants and projects, please contact our sales manager Mr. Ulrich Bucher bucher@extrutec-gmbh.de
News

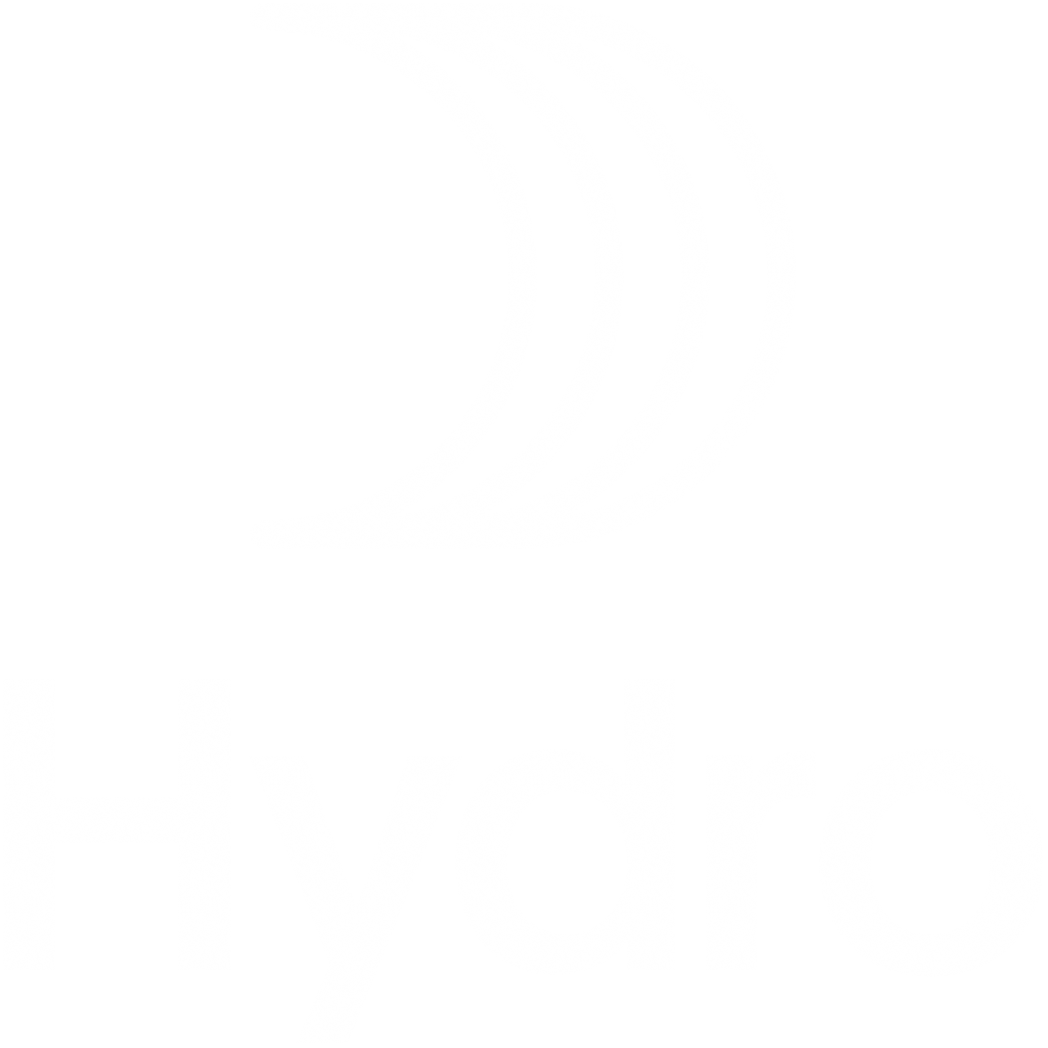
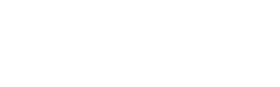
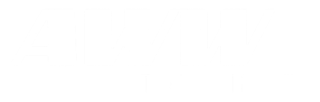
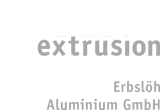

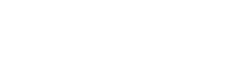
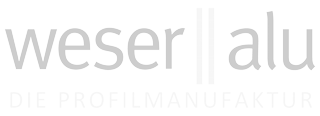
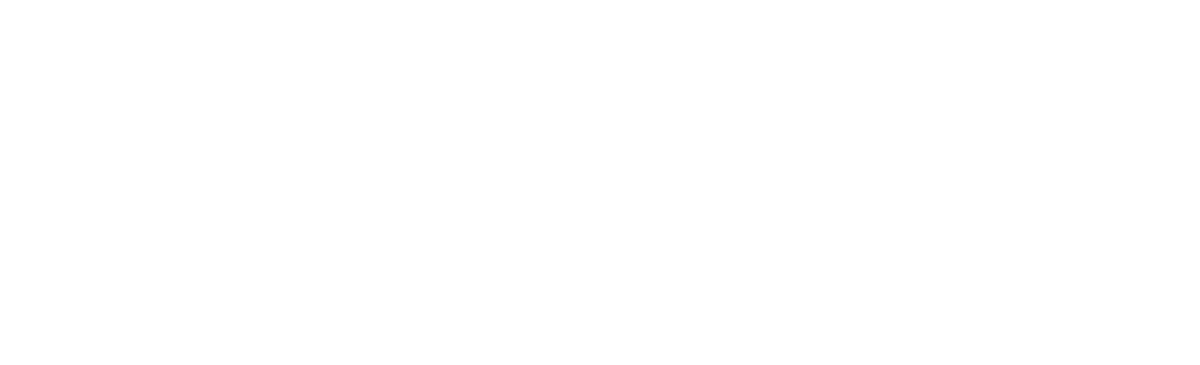